Company Safety Rules and Practices
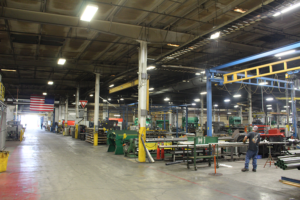
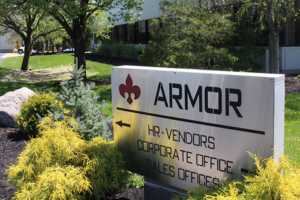
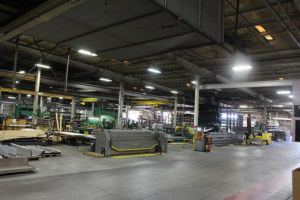
1. Employees and visitors are required to report all injuries and/or unsafe conditions to their area Supervisor or
Manager on duty ASAP. You can also report issues to the Environmental, Health, and Safety (EHS) Manager.
A Near Miss/Hazardous Condition Report should be completed & forwarded to the EHS Manager.
2. Employees and visitors are required to wear safety glasses with side shields in the manufacturing Plant or large
safety glasses over street glasses. The only exceptions are individual offices, restrooms, and the lunchroom,
located within the manufacturing plant.
3. Due to the nature of our business, and our effort to ensure your safety, please be aware, under no circumstances
are open-toe/open-back shoes or sandals permitted anywhere on the Manufacturing floor.
4. Be aware of your surroundings at all times observing forklift and overhead crane movements.
5. Be aware of your nearest First Aid Cabinets, along with nearby Eyewash Stations, Fire Extinguishers, and Pull Stations.
6. Know your Evacuation Zone Number and your nearest exit. See your Supervisor or the EHS Manager for
Zone Number for your area.
7. When working or walking in areas where grinding/welding occurs, please utilize weld curtains. Keep all combustibles
out and away from the area. Sparks travel a long distance and are a fire hazard. If you see a combustible
(anything that leaves ash), please safely remove it immediately.
8. Employees must use correct personal protective equipment (gloves, safety glasses, sleeves, face shields,
chemical aprons, welding jackets, and welding sleeves) for tasks as required. If you have questions regarding
what to use, or which type is required, please ask your Supervisor or the EHS Manager. Safety glasses and
safety shoes are required for all manufacturing employees and by other employees within the manufacturing areas.
9. Employees must maintain clear aisles, walkways, stairways, emergency exits, and other designated areas and
provide unobstructed access to control/electrical panels and all emergency equipment. Do not block any of these
items. Please follow the 3′ rule! There must be 3’ of clearance in all directions, to the side, front & back as a guide.
10. All personal electronic devices (cell phones or any other electronic device) may not be used while operating
manufacturing machinery (i.e., press and shear &/or driving equipment such as forklifts.
11. Chemicals must be handled using safe work practices and in an environmentally responsible manner.
Chemical containers must be covered and clearly and appropriately marked. Do not leave lids off any containers.
The only time a lid should be off is when someone is actively putting a chemical in or taking a chemical out. Waste
paint containers must have the bungs removed when put in the hazardous waste storage room to allow for off-gassing.
If you have questions, please ask your Supervisor or the EHS Manager.
12. Safety guards and/or devices may not be altered, bypassed, or removed from machinery or equipment.
Follow established lock-out/tag-out procedures before proceeding with repairs or non-routine tasks.
If you have questions, please contact your Supervisor or the EHS Manager.
13. Employees must operate all Company equipment (this includes forklifts/material handling equipment, tools, etc.)
in a safe manner, which does not endanger themselves, other employees, or equipment.
14. Area-specific housekeeping practices are in place to ensure safe working conditions. Please assist in keeping
your area(s) clean and organized, this includes break area(s). Please keep aisles and walkways clear.
Do not block exits.
15. Do not walk on pallets or potentially unsafe surfaces.
16. The use of, possession of, or being under the influence of alcoholic beverages, illegal drugs, or intoxicating
substances while on the job or on company property is strictly prohibited. ARMOR is a nicotine/drug-free campus.
17. Smoking, oral tobacco, and nicotine use of any kind, including electronic cigarettes are prohibited in all U.S.
Armor owned and/or leased properties; including all internal and external areas, parking lots, entrances and
exits, and company vehicles. ARMOR is a nicotine/drug-free campus.
18. Employees must always comply with federal, state, and local laws as well as employer regulations,
safety programs and company policies.
Questions should be referred to your area Supervisor or the EHS Manager.
The Armor Group is a Member Vendor of ISN, a global leader in contractor and supplier information management. ISN’s global platform with data-driven products and services helps companies manage risk and strengthen relationships. ISN’s goal is to promote continual improvement in contractor management and strive for a safe work environment for everyone.